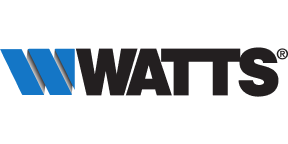
Integrated chip detection at Watts Industries Germany
Challenge
Chips (swarf) on the threads of underfloor heating manifold pipes cause leaks and require reworking or generate rejects. Manual spot checks are inefficient. Defective workpieces indicate wear on the machining tools, for example, so early detection is crucial. Every further process step with defective workpieces causes unnecessary costs. The aim is to automatically detect chips (swarf) on the workpiece within a few seconds without prolonging the overall process.
How we helped
We developed a pick-up station for distribution pipes with Watts and collected images of faulty and defect-free workpieces. With this data, an AI model for automatic chip recognition was trained and evaluated. After successful integration into the production process, the AI model enables efficient and reliable quality control.
Working with prenode has given us an efficient solution for automated chip recognition in fully automated manufacturing plants. AI-based testing increases our quality and saves valuable resources.
- Andreas Becker, Lean, Industrial Engineering & EHS Manager, Watts Industries Germany
Results
Significantly less waste:
The introduction of automated chip (swarf) recognition leads to a significant reduction in the scrap rate.
Increased productivity:
Automatic 100% control immediately detects faulty parts and prevents waste, increasing productivity.
Higher overall process quality:
The number of faulty workpieces that go through the entire production process is noticeably reduced, meaning that scrap costs have been significantly reduced.
Video: Microsoft Intelligent Manufacturing Award 2023 | Meet the winners
Company:
Watts Industries Deutschland GmbH
Description:
Watts is a leading provider of innovative products for hot water heating systems.
Founded
1960
Industry:
Production in the field of heating and air conditioning technology
HQ:
Landau, Germany
Are you looking for support in building your AI application?
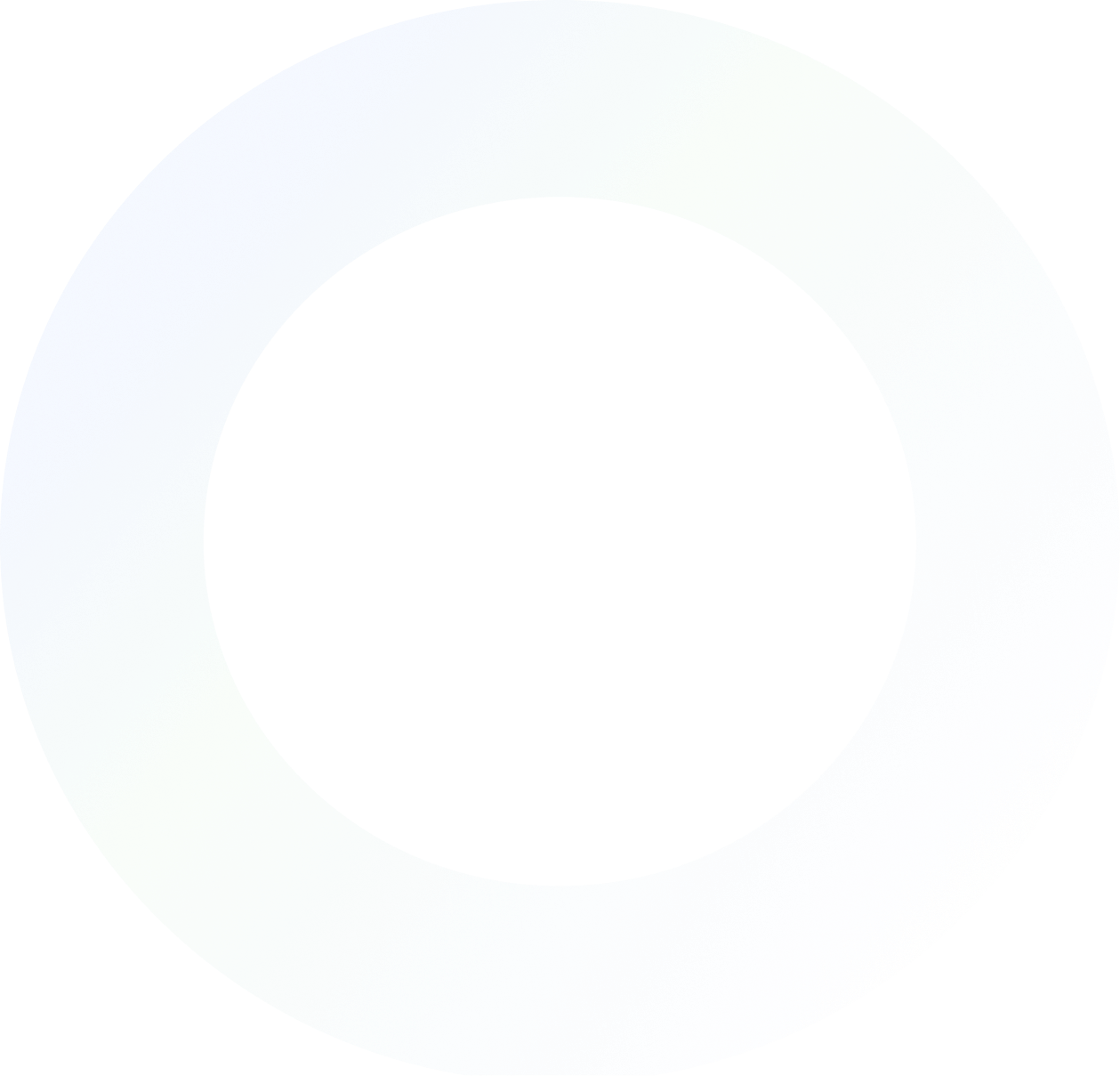